Can Rapid Aluminum Injection Molds Replace Traditional Steel Molds?
When we think about injection molds, the first thing that usually comes to mind is the heavy and expensive steel mold. While steel molds are known for their durability and precision, aluminum molds have gained attention for their low cost and quick turnaround, especially in specific applications. In this article, we will explore whether aluminum molds can truly replace traditional steel molds in the injection molding process.
Steel Injection Molds
1. What is a Steel Mold?
A steel injection mold is a common type of mold used in the plastics processing industry. These molds are primarily made from various types of steel (e.g., P20, H13, S7) and are used to produce high-quality plastic components by injecting molten plastic into the mold. Steel molds are widely used in mass production scenarios due to their strength and durability.
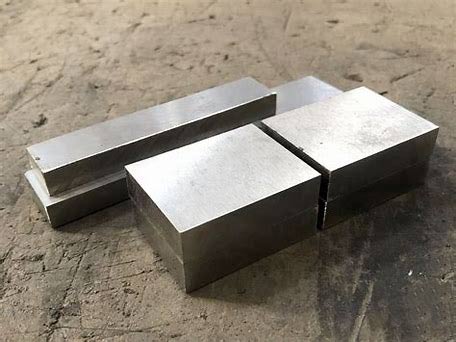
2. Advantages of Steel Molds
- Durability and Strength: Steel molds offer excellent hardness and strength, allowing them to withstand the high temperatures and pressures involved in the injection molding process. This makes them ideal for long-term use.
- Wear Resistance: Steel molds are highly resistant to wear, maintaining their precision and shape even during high-volume production runs.
- Thermal Stability: Steel molds provide good thermal stability, minimizing the risk of deformation due to temperature fluctuations, thereby improving production efficiency.
- Precision Machining: Steel’s machining capabilities enable high-precision engraving and intricate mold designs, ensuring detailed and accurate components.
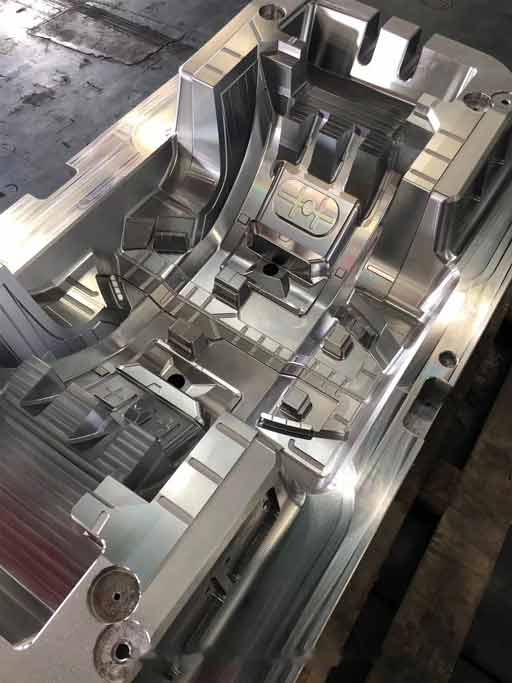
3. Disadvantages of Steel Molds
- Complex Manufacturing and High Cost: Steel molds require complex machining and advanced equipment, which can lead to high manufacturing costs.
- High Maintenance Costs: Steel molds must be regularly maintained to prevent issues such as rust or wear, which adds to the overall operating costs.
- Less Flexibility: Due to the long lead times and high costs, steel molds are less suitable for small batch production or designs requiring frequent changes.
Aluminum Injection Molds
1. What is an Aluminum Mold?
Aluminum injection molds are made from aluminum alloys and are often used for rapid prototyping or small production runs. Due to their lightweight nature and ease of machining, aluminum molds are increasingly seen as a cost-effective alternative for certain applications.
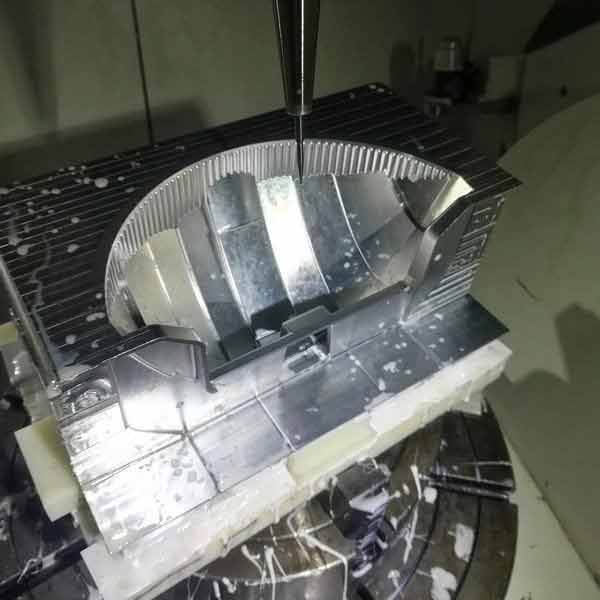
2. Advantages of Aluminum Molds
- Lightweight: Aluminum molds are significantly lighter than steel molds, making them easier to transport, install, and handle—especially in environments where molds need to be changed frequently.
- Faster Machining: Aluminum can be processed more quickly than steel, meaning shorter lead times from design to production, making it ideal for rapid prototyping and short-run production.
- Good Thermal Conductivity: Aluminum has excellent thermal conductivity, allowing for faster heat dissipation, which helps in controlling the temperature of the mold during production and improving product quality.
- Lower Cost: Aluminum molds are generally less expensive to manufacture, especially for small-scale production, reducing the overall investment risk.
- Easier to Repair and Modify: Aluminum is easy to machine, making repairs and modifications simpler and faster when compared to steel molds.
3. Disadvantages of Aluminum Molds
- Lower Durability: Aluminum molds are less durable than steel molds, particularly under high-temperature or high-pressure conditions, which can lead to a shorter lifespan.
- Prone to Wear: Aluminum is softer than steel and more prone to wear, making it less suitable for high-volume production runs where frequent maintenance or replacements may be required.
- Not Suitable for High-Temperature Materials: Aluminum’s lower resistance to high temperatures limits its use in molding certain high-temperature engineering plastics.
- Insufficient Strength for High Pressure: Under high-pressure injection molding environments, aluminum molds may deform, affecting the precision of the molded parts.
How to Choose Between Steel and Aluminum Injection Molds
1. Cost Analysis
- Steel Molds: While the initial investment for steel molds is high, their durability and strength make them cost-effective in high-volume production, reducing the per-part cost over time.
- Aluminum Molds: Aluminum molds are more suitable for small-scale or rapid prototyping applications due to their lower initial cost. However, frequent replacement due to wear can drive up costs in the long term.
2.Mold life
Steel Mold Lifespan
- Steel molds are ideal for high-volume production due to their long lifespan. They can typically handle 500,000 to over 1 million injection cycles, depending on the quality of the steel, mold design, and maintenance. The high strength and wear resistance of steel allow it to withstand continuous high-pressure, high-temperature conditions, making it suitable for long-term, large-scale manufacturing.
Aluminum Mold Lifespan
- Aluminum molds, on the other hand, have a shorter lifespan, usually completing 5,000 to 100,000 injection cycles, depending on the type of aluminum and the production environment. The shorter lifespan is due to aluminum’s lower resistance to wear and heat, making it more appropriate for small-batch production and rapid prototyping.
3. Production Needs
- Steel Molds: Steel molds are ideal for high-precision, large-scale production, such as automotive components, medical devices, and appliance housings.
- Aluminum Molds: Aluminum molds excel in small-batch production and rapid prototyping, where quick turnaround and lower costs are essential, such as in consumer electronics and medical devices.
4. The Impact of Emerging Technologies
Advancements in 3D printing have provided new possibilities in the mold-making process, especially for small-batch production and rapid prototyping. 3D printing allows for greater flexibility in mold design and material selection, which can complement traditional mold manufacturing methods. For complex shapes or rapid design iterations, 3D printing offers significant advantages, especially when combined with aluminum molds for quick modifications.
Conclusion: Can Aluminum Molds Replace Steel Molds?
In conclusion, both aluminum and steel injection molds offer distinct advantages depending on the production requirements. Steel molds remain the preferred choice for high-volume, high-precision, and long-term production due to their durability and strength. Aluminum molds, on the other hand, provide a cost-effective alternative for rapid prototyping and small-batch production, thanks to their lower cost and faster manufacturing times. Rather than replacing steel molds entirely, aluminum molds serve as a complementary solution for specific use cases where speed and flexibility are prioritized.